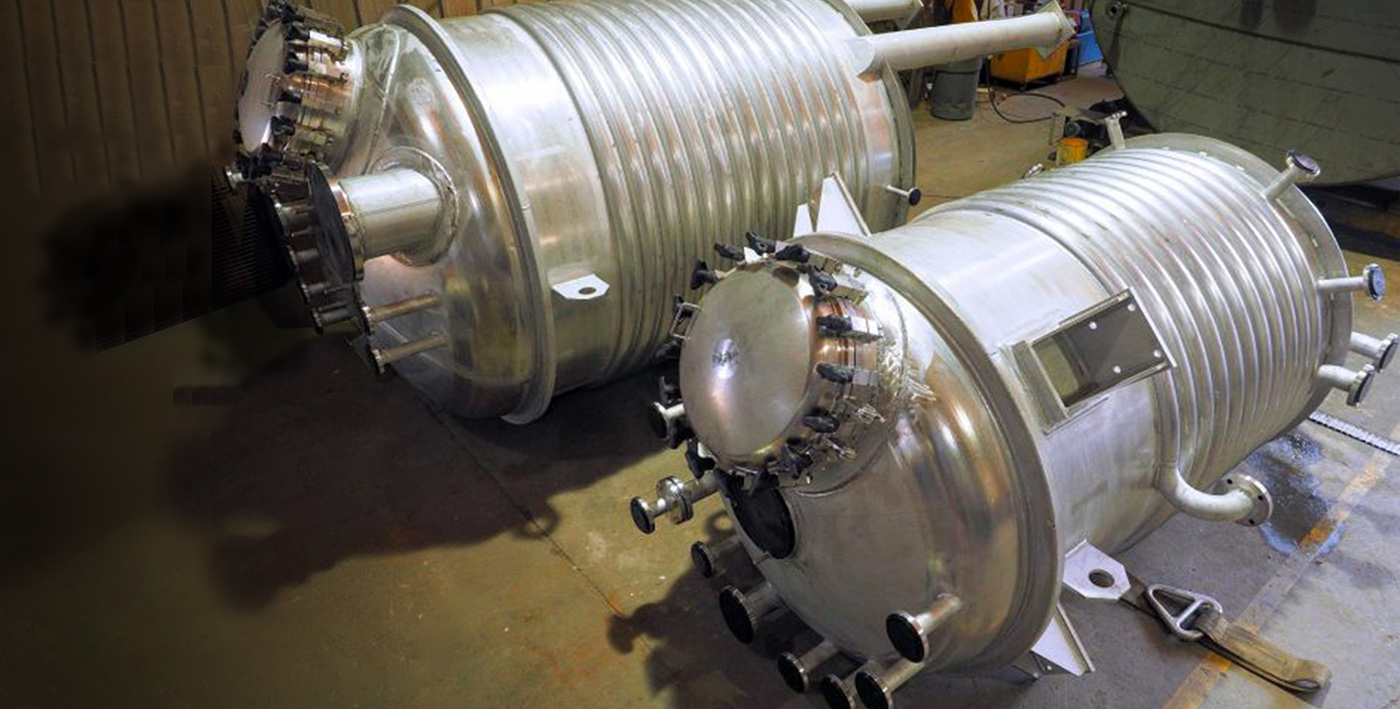
Blasting, Polishing & Passivation
External & Internal Vessel Finishes
Blasting, Polishing & Passivation
EXTERNAL & INTERNAL VESSEL FINISH OPTIONS
As process vessel and equipment fabrication specialist, Bendel can advise on various internal and external finish options and help you select the best solution for your particular process.
We provide our clients with a wide range of finish options achieved through various methods including sand blasting, glass bead blasting, passivation, and polishing. Questions? Send us an inquiry here or contact us by phone to learn more: (+1) 866.596.5112
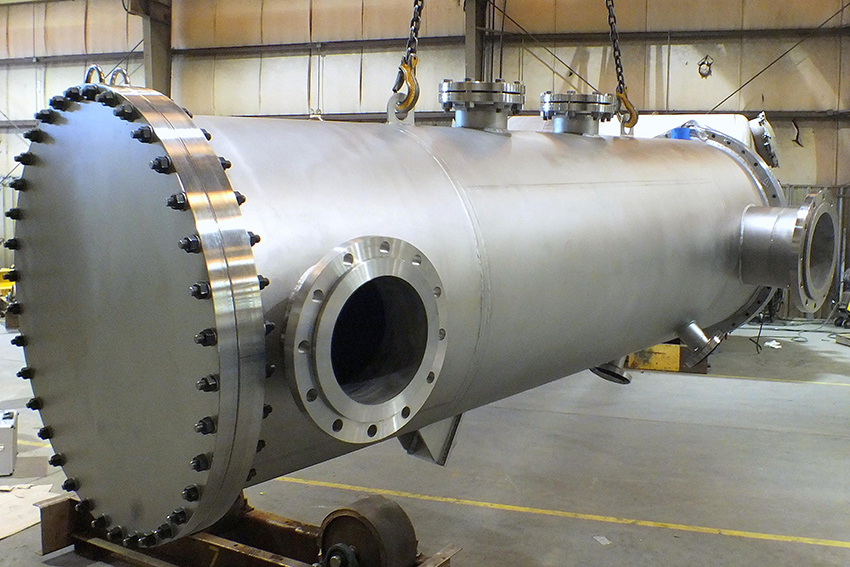
SAND BLAST
Sand blasting, also known as abrasive blasting, is commonly used as a way to prime metal surfaces prior to the application of coatings. This process prepares tanks and vessels with the ideal surface profile for effective coating adhesion and delivers optimal bonding - and lasting performance.
Sand blasting can also be used for removing existing coatings and/or as a finishing step for removing burrs, mill scale, trace rust and other potential contaminants in addition to providing a desired rough surface textured finish.
Headline
Add your content here.
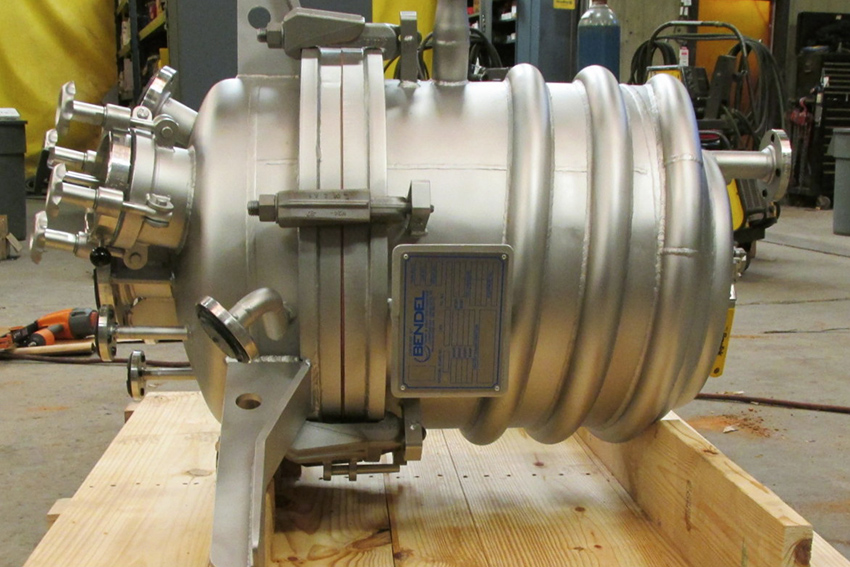
GLASS BEAD BLAST
Glass Bead blasting is sometimes confused with sand blasting, but generally refers to the use of micro beads or spherical materials such as glass or ceramic beads, aluminum oxide, and silicon carbide, rather than the 'grit' used in sand blasting.
Bead blasting leaves a more uniform finish that is less coarse than abrasive (sand) blasting, and delivers a soft, bright finish. Fine bead blasting is typically used when a ‘satin finish’ is desired, while courser beads can be used to deliver a uniform, but somewhat rougher finish.
Headline
Add your content here.
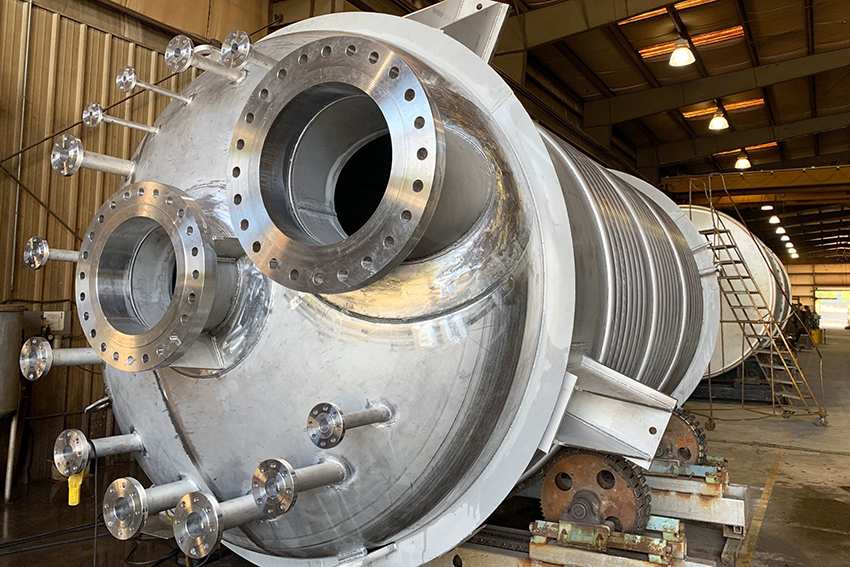
PASSIVATION
Pickling and Passivation is a chemical process that is used to alter the surface of stainless steel to make it more resistant to rust. During the passivation process, metal is methodically bathed in an acid solution (citric or hydrochloric acid) which removes any impurities along with microscopic free iron from its surface, leaving behind its remaining alloys (typically chromium and nickel) to form a corrosion-resistant ‘passive film’ at the surface of the underlying steel.
Passivation also perfects the metal’s surface by removing any weld burns, and results in an even, satin finish.
Headline
Add your content here.
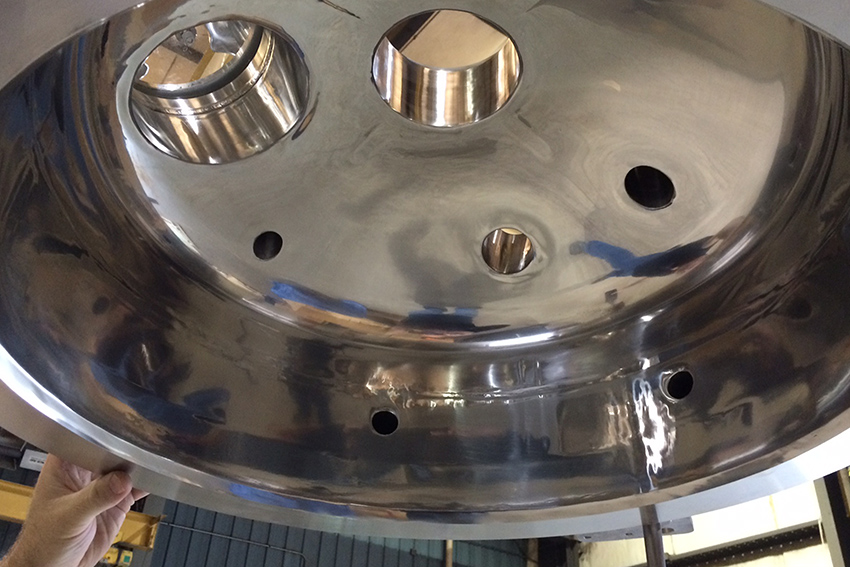
POLISHING
Polishing is a process that enhances the surface of tanks, vessels and other equipment, using an abrasive belt or wheel, or through a mass finishing process such as tumbling. While polishing methods vary, all methods involve some level of surface removal. Polishing can be used to enhance the final surface of a finished product or it can be used for surface preparation prior to the application of a high-performance coating.
Polishing can be combined with final buffing processes to achieve a bright, mirror-like finished surface.
Headline
Add your content here.
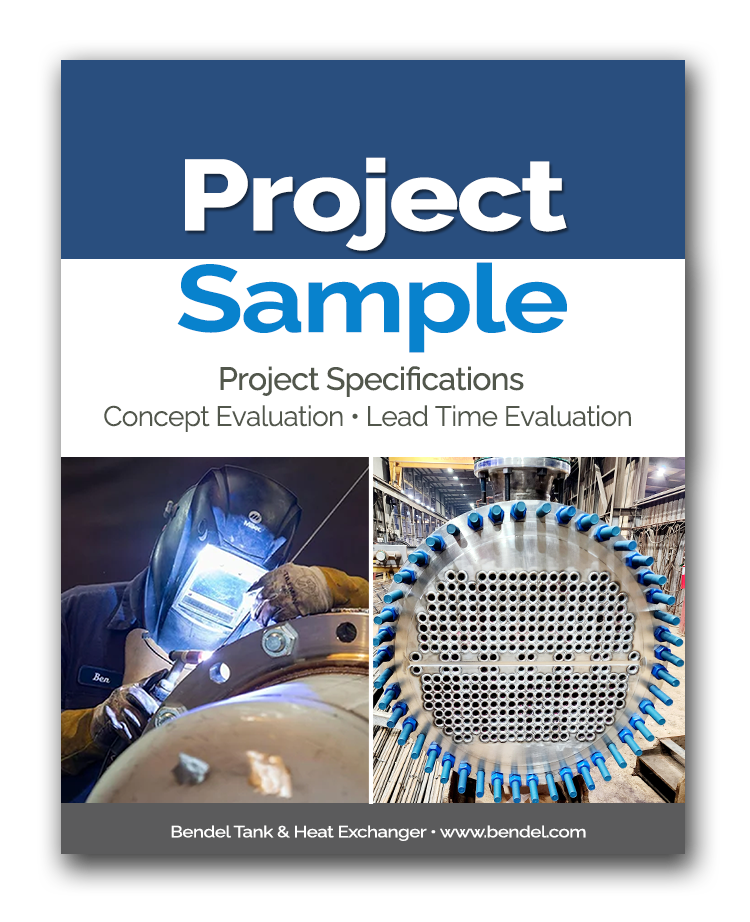
FREE: Project Sample
Receive a complete sample Bendel project proposal, including:
- Complete sample project budget
- Complimentary concept evaluation
- Lead time evaluation
- Cost analysis
- More...